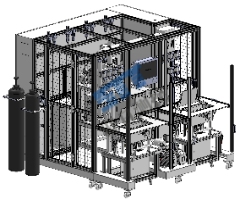
In the booming development process of the modern automotive industry, the high-pressure common rail technology of traditional fuel vehicles has greatly improved the fuel injection accuracy and combustion efficiency, thereby enhancing the engine's power performance, reducing fuel consumption and emissions. This technology has also achieved excellent performance in the application of new energy extended-range hybrid vehicles. The pressure has continuously increased from the initial 15 MPa to 65 MPa. The processes and technologies of components such as fuel common rails, fuel inlet pipes, and fuel injection system assemblies have all made great progress. However, to achieve these advantages, the high-pressure common rail system must maintain a high degree of tightness. Because any tiny leak may lead to unstable fuel pressure, affect injection accuracy, reduce engine performance and reliability, and even bring safety hazards.
CO₂ air conditioning, as an environmentally friendly automotive air conditioning system, has many advantages. Firstly, CO₂, as a natural refrigerant, has minimal impact on the environment, does not damage the ozone layer, and its global warming potential is much lower than that of traditional refrigerants. Secondly, the CO₂ air conditioning system has higher cooling efficiency and can provide stronger cooling effect at lower energy consumption. However, the CO₂ air conditioning system needs to operate at a state of 17 MPa, which imposes extremely strict sealing requirements on the compressor, valves, air conditioning pipes, and assembly connections of the air conditioning system. Once there is a leak, it will not only reduce the cooling effect but also may cause adverse environmental impacts.
With the continuous growth of the global demand for clean energy, the application of hydrogen energy in the automotive field is attracting increasing attention. Hydrogen fuel storage tanks, as one of the core components of hydrogen energy vehicles, have significant development significance. Hydrogen fuel has advantages such as high energy density and no pollution, and can provide efficient and clean power for vehicles. However, due to the flammable and explosive characteristics of hydrogen, its storage and transportation require a high degree of safety. Hydrogen fuel storage tanks need to have extremely high tightness at a state of 70 MPa to prevent safety accidents caused by hydrogen leakage.
To ensure that these products with extremely strict leak control are detected in time during the manufacturing process, the development of high-pressure and ultra-high pressure leak detection equipment is of great significance. Helium leak detection testing has been proven to be a reliable method. STT has been involved in this process since 2010. In the past 15 years, the leak detection systems developed from 15 MPa to 70 MPa have been widely used in various industries, and have accumulated many unique technologies in high-pressure leak detection.
Compared with traditional pressure detection systems, high-pressure systems face huge technical challenges, mainly in the following aspects: generation of high pressure, effectiveness of high-pressure components, helium loss during the testing process, stability of high-pressure test fixtures, and test range of equipment. STT uses gas booster pump technology to achieve a maximum pressure output of 75 MPa. Equipped with the STT-H-RE booster recovery software, its algorithm combines functions such as concentration ratio, helium replenishment strategy, precise pressure control, and helium backfilling during gas boosting, completely avoiding helium loss during the boosting process and saving a large amount of helium usage cost for users. In fact, it is not enough for high-pressure test systems to only focus on recovery rate. Paying attention to helium loss rate is the key to evaluating the comprehensive performance of a system. For example, taking a 25 MPa fuel common rail as an example, a system using other technologies can only test 10,000 pieces with a 15 MPa, 40L helium bottle, while the STT-H-RE system can test 20,000 pieces, saving 50% of helium cost for users.
High-pressure reliable sealing is another extremely challenging technology for this test system. STT has unique technologies in aspects such as power output in the vacuum test chamber, digestion of component tolerances, replacement frequency of sealing elements, and ensuring no damage to components during the testing process. If these technologies are not mastered, the test vacuum chamber will be large in volume, with complex internal joints and pipelines, unable to achieve automatic clamping, and large sealing element loss, thus affecting the efficiency and stability of this system. Users usually evaluate the ability of this system by evaluating what brand of vacuum system and what brand of tester are used. In fact, using these components can only ensure the realization of the basic functions of the system. For reliability, solution providers need to have core technical accumulation and capabilities tailored to user needs.
STT has a 70 MPa high-pressure fuel common rail test capability, which is currently the highest helium leak detection pressure test system known. The 17 MPa compressor and air conditioning pipe test system of the CO₂ air conditioning system are both in operation. In addition, a hydrogen tank test system with an output pressure of 80 MPa has been developed in cooperation with leading customers.
In conclusion, the continuous innovation of STT's ultra-high pressure helium leak detection equipment in the applications of high-pressure fuel common rails, CO₂ air conditioning, and hydrogen fuel storage tanks has made important contributions to the development of the automotive industry. It is believed that with the continuous efforts of STT, ultra-high pressure helium leak detection equipment will play a more important role in the detection field of these key automotive parts and provide strong support for the high-quality development of the automotive industry.