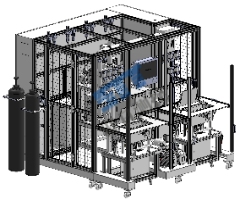
A basic vacuum system is composed of three essential components: Vacuum pump, vacuum chamber and vacuum valve. The vacuum valve selection is central to optimizing the performance of the vacuum system and is influenced by a wide range of criteria. Vacuum valves can be divided into two categories:
Our selection of isolation valves includes several varieties, including angle and in-line valves, gate valves, isolation pendulum valves, and ball valves. These valves are either manually or pneumatically operated. The pneumatic valves include options to include a position indicator to provide the system with open and close information. They can also include a solenoid used to open and close the pneumatic air supply to control the valve functionality. Our vacuum valves are available in aluminum or stainless steel, to meet a wide range of needs.
Angle valves are often used in applications to isolate gas flow through the forelines of the vacuum system. In contrast, gate and pendulum valves are often used to isolate a vacuum pump from the vacuum chamber. Gate valves can also be used in systems with vacuum lines larger than DN 100. Our vacuum valves are suitable for a wide range of applications in Semiconductor, Industry, Analytics, and R&D applications.
The pressure control valve category includes a selection of butterfly valves and pendulum valves.
A complete pressure control system is composed of three essential components: a valve, a controller, and a pressure gauge. The primary function of pressure control valves is to regulate the pressure inside a vacuum chamber and regulate gas flow within vacuum systems. These products are suitable for applications that require precision process control such as those in the semiconductor and coating sectors.
Criteria to find a suitable vacuum valve for your application
Functional purpose of the valve: The desired application significantly influences the selection of the valve. The requirements vary depending on whether the valve is primarily to open and close vacuum lines or to regulate pressure.
Installation space and system compatibility: The physical dimensions of the available installation space and the flanges of the pump and chamber have a direct influence on the selection of the appropriate valve size.
Gas influences: The composition of the gases flowing through the valve strongly influences the choice of materials. The right choice of materials ensures the durability and reliability of the valve.
Temperature conditions: Knowledge of the expected temperatures is essential in order to select the appropriate materials for the valve body and seals, and thus guarantee long-lasting functionality.
Pressure: Understanding the pressure conditions the valve will be exposed to influences the valve selection.
in different pressure ranges
Vacuum valves can be used in both high vacuum and ultra-high vacuum applications. Which valve to select can be determined by sealing technology. For high vacuum pressures of 1x10-8 hPa, Pfeiffer Vacuum has an extensive selection of valves with a elastomer seals and ISO-KF/ISO-K flanges. For ultra-high vacuum applications, opt for a valve with a metal seals in the wetted areas and CF flanges. Additional options include an all-metal valve, in which all the seals are metal.
Valves are activated in a variety of ways. Isolation valves are generally operated manually or pneumatically, while pressure control valves function via an electric motor.
Pneumatically operated valves use compressed air to actuate the valve. The required compressed air pressure flowing into the valve’s air cylinder is often between 4 and 8 bar to move the valve. Some valves, generally smaller angle valves, are "single-acting," meaning that the compressed air is used to move the valve into position. When compressed air is lost, a spring is used to move the valve into the default position. Usually, valves are “normally closed”, with the actuator moving into the open position and the spring closing the valve. On the other hand, larger valves are generally “double-acting”. In this case, compressed air is used to drive the valve both open and closed. In order to control the flow of compressed air, a solenoid is used to release the air to the valve air cylinder. Electromagnetic valves come with this solenoid built into the valve. Most vacuum systems require a 24 V DC powered solenoid to control the compressed air line.
Valves are also available with options to include a position indicator to indicate whether a valve is open or closed. For manual valves, the position can be seen by a visual indicator. The position indicator on a pneumatic valve sends feedback directly to the vacuum system about the position of the valve.